The E-2D Advanced Hawkeye is redefining mission excellence, evolving with capabilities in an increasingly complex battlespace.
Fast-Tracking the Future
Revolutionizing Aircraft Engineering Through a Digital Ecosystem
Northrop Grumman is transforming aircraft development through its investment in digital engineering, creating a seamless digital ecosystem that connects design, manufacturing and testing. That progress took a major leap forward with the first flight of the Model 437 — a test plane with wings designed and built entirely through Northrop Grumman’s connected digital process, known as Digital Pathfinder.
The milestone shows how digital engineering can speed up timelines, lower costs, and improve accuracy over the lifetime of an effort. With the help of a fully connected digital ecosystem, Northrop Grumman creates a single digital thread where teams can collaborate in real-time. This helps teams spot and solve issues before production begins, offering a window into the future of aircraft engineering.
“Our digital environment provides near-real-time visibility, creating a single source of truth,” said Sarah Beaudin, Director, Digital Pathfinder at Northrop Grumman. “This allows us to adopt a shift-left approach — iterating everything from design through sustainment as early as possible in the program. By the time we actually start building things, we’ve already got it right.”
Digital Ecosystem of the Future
The goal was to develop a low-cost, multi-purpose aircraft using a comprehensive digital thread from start to finish. Northrop Grumman worked on the design and manufacturing of the wings, while Scaled Composites focused on the rapid design, fabrication and test of an aircraft platform to demonstrate the wings. This teamwork improved both efficiency and innovation.
The results were impressive. Less than 1 percent of the wing design required rework compared to the industry average of 15 to 20 percent. The project also experienced less than a 2 percent delay in its schedule. These results show how a digital ecosystem can improve timelines while reducing errors.
The team also highlighted how digital engineering can improve manufacturing. A key advancement is determinate assembly, which ensures parts arrive perfectly aligned and ready for assembly, cutting down on costly errors. Precise digitally based tooling designs save time by optimizing the tool and manufacturing operations before ever drilling the first hole.
Ultimately, this technology allows for more creative designs. Engineers can try complex shapes and materials that traditional methods cannot handle. Flexibility is a critical benefit of digital engineering.
Scaling Across the Enterprise
The Digital Pathfinder team was small, agile, and empowered to take leaps ahead in methods of testing and stressing the integrity of the digital thread. While its first tangible output was a set of wings and a new technology demonstrator, the process showed that it can operate efficiently and effectively, and, be shared and replicated across the enterprise.
“Digital Pathfinder enabled us to integrate and optimize our digital systems, boosting productivity and minimizing wasted time,” Sarah said. The company is incorporating digital capabilities, tools and lessons learned across highly complex programs.
“The digital thread that is connecting our tools and the digital systems engineering process embedded in our models are scalable to large programs, and the lessons learned are going to pay huge dividends.”
Learn more about how digital ecosystems are revolutionizing the way we do business.
Related Programs and Stories
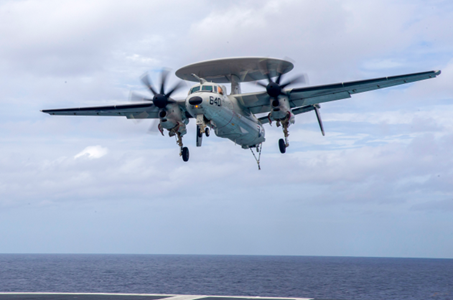
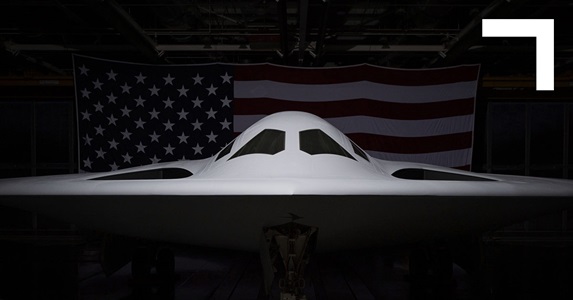
10 Facts About the B-21 Raider
The Raider provides the Air Force with long range, high survivability and mission payload flexibility
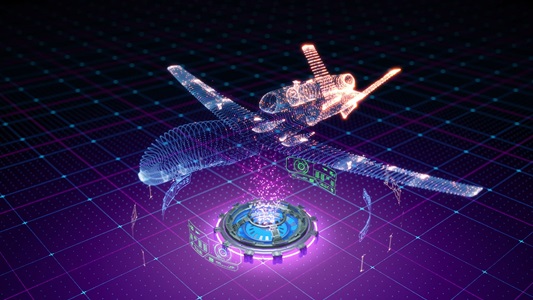
Digital Transformation
Our digital ecosystem connects customers, suppliers, and employees, streamlining operations and boosting innovation throughout the program lifecycle.